Veritas Case Study – NorthStar Medical – Veritas plays critical role in first-of-its-kind radioisotope facility

PROJECT
NorthStar Medical Radioisotopes LLC – Isotope Processing Facility
LOCATION
Beloit, WI, USA
GC/PROJECT MANAGER
CCI – Corporate Contractors, Inc.
VERITAS SCOPE OF WORK
Design, construct and install radiation shielded vault and shielded doors to house IBA 40 MEV TT300-HE accelerators and surrounding rooms
BUILD SITE
Inside new production building
COMPLETED
2021
Recognized as one of Wisconsin’s most impressive and unique construction projects in 2020.
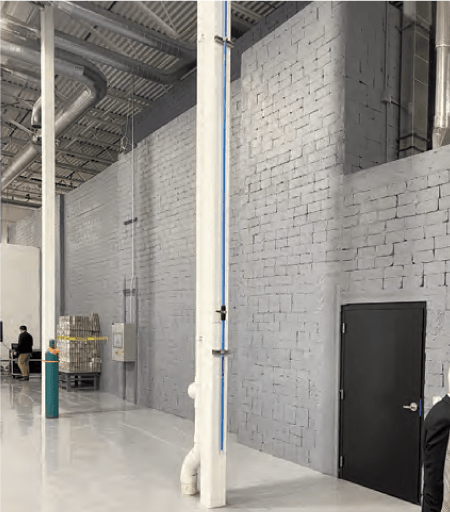
The Project
NorthStar Medical Radioisotopes is poised to become the first-in-class production supply chain for future therapeutic radiopharmaceuticals. In September 2019, NorthStar broke ground on a 30,000 square foot (2787 m2) manufacturing building to house its first pair of IBA Rhodotron® accelerators.
A radiation shielded vault had to be constructed inside this building to shield the IBA 40 MEV TT300-HE accelerators and surrounding rooms. These rooms would support NorthStar’s innovative Mo-99 production and require some walls of Veritas VeriShield® high density modular shielding to be over 7 feet thick (2133mm) and up to 25 feet high (7620mm).
The Veritas design team needed to design this industrial solution to meet not only space requirements, but also structural and radiation shielding requirements.
The Solution
Veritas ultra-high density VeriShield® modular shielding was selected to provide the radiation protection for the high energy accelerators, as well as the structural support for the vault. The dry-stacked VeriShield modules would allow for design adjustments and the ability to build this large shielded vault in a space where it would be impossible to build with concrete. The engagement of Veritas’ in-house team of engineers, physicists, project managers and construction specialists would also expedite delivery and ensure success for NorthStar.
The removable Veritas VeriShield® modular shielding would allow the facility to meet Wisconsin’s requirement of being able to dismantle and decommission the vaults, unlike typical poured concrete. And, with multiple trades working onsite, the off-site manufacturing of the Veritas shielding would allow concurrent construction schedules, resulting in faster installation, less site disturbance and greater safety.
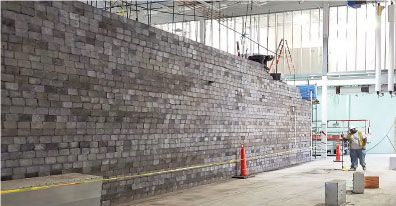
Equipment Access and Additional Mobilizations
The installation of the IBA equipment required transport openings to be integrated into the shielded walls to allow ingress of the cyclotrons and other equipment. Multiple openings were left in the modular shielding of both Rhodotron rooms as well as the water skid rooms.
Following placement of the equipment, Veritas remobilized to quickly seal all openings to prevent radiation leakage and complete the shielding installation.
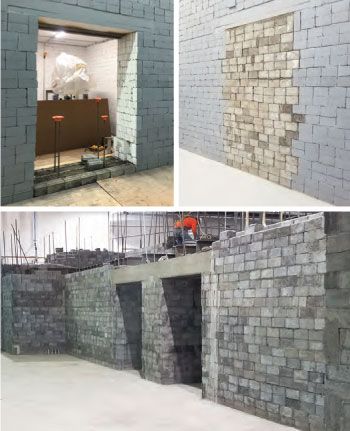
The Challenge
The time schedule to build the approximately 6,000 square foot (557 m2) shielded vault was aggressive. The large radiation-protective structure would be constructed inside the new building structure with limited access, and had to be completed in time for the scheduled IBA equipment arrival. There would also be the added complexity of multiple trades working onsite simultaneously in order to meet the tight construction deadlines.
Covid protocols, and their effects on the workforce, also had to be dealt with.
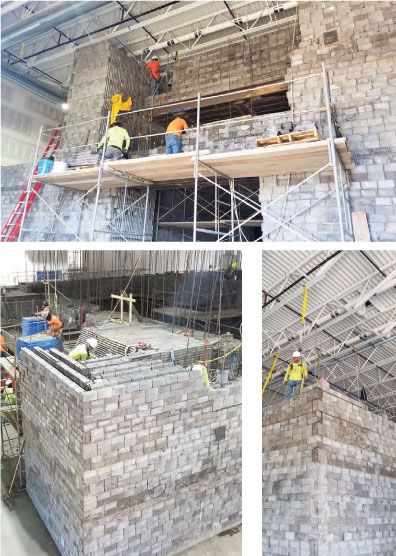
The Results
The Veritas vault construction was completed ahead of schedule and with the necessary access required for the IBA TT300-HE machines. IBA was able to use the integrated vault transport openings to conveniently bring the equipment into the structure.
Following the IBA equipment installation, Veritas remobilized and infilled all transport openings with VeriShield® to provide uninterrupted radiation protection. The VeriShield® walls and ceiling beams also provided the structural support necessary for interior cranes.
Utilizing VeriShield® V250 modular shielding also provided other impactful results. The challenge of a limited amount of working space above the vault ceiling was solved with an installation sequence that provided for the safe and efficient placement of the top courses of shielding. Veritas was also able to accommodate and install multiple shielding penetrations, including those for the oversized HVAC systems and a telescopic sleeve located in the target room, at precise locations and heights.
Utilizing VeriShield® V250 modular shielding also provided other impactful results. The challenge of a limited amount of working space above the vault ceiling was solved with an installation sequence that provided for the safe and efficient placement of the top courses of shielding. Veritas was also able to accommodate and install multiple shielding penetrations, including those for the oversized HVAC systems and a telescopic sleeve located in the target room, at precise locations and heights.
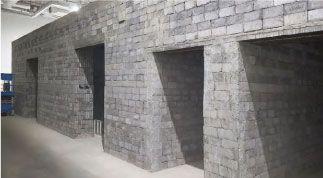
The Results
Custom Veritas radiation shielding sliding SmartDoors® were installed, providing full radiation protection and meeting all required safety and security protocols.
The Veritas team was also able to overcome the Covid virus, and the installation crew was able to complete the project well ahead of schedule.
NorthStar is now revolutionizing the production of concentrated molybdenum-99. Their game changing production method allows for higher activity source vessels without the use of uranium, making Mo-99 more widely available across the U.S.